-
Location
Level 4, 20 Hunter Street, Sydney
-
Completed
June 2020
-
Architect
Todd Hammond
-
Area
2,000sqm
-
Type
Fitout
-
Delivery Type
Fixed Lump Sum
-
Duration
28 weeks
-
Project Manager
Kernel and CBRE
-
Value
$3M - $5M
Challenging the norm
The traditional law firm; a space where function supersedes form, and aesthetics are confined to client facing spaces. Enter Swaab.
Replete with technical construction feats, extraordinary quality of finish, and flexible infrastructure to support their evolving business needs, Swaab’s Sydney office fitout is a rare counterpoint to its rigid industry.
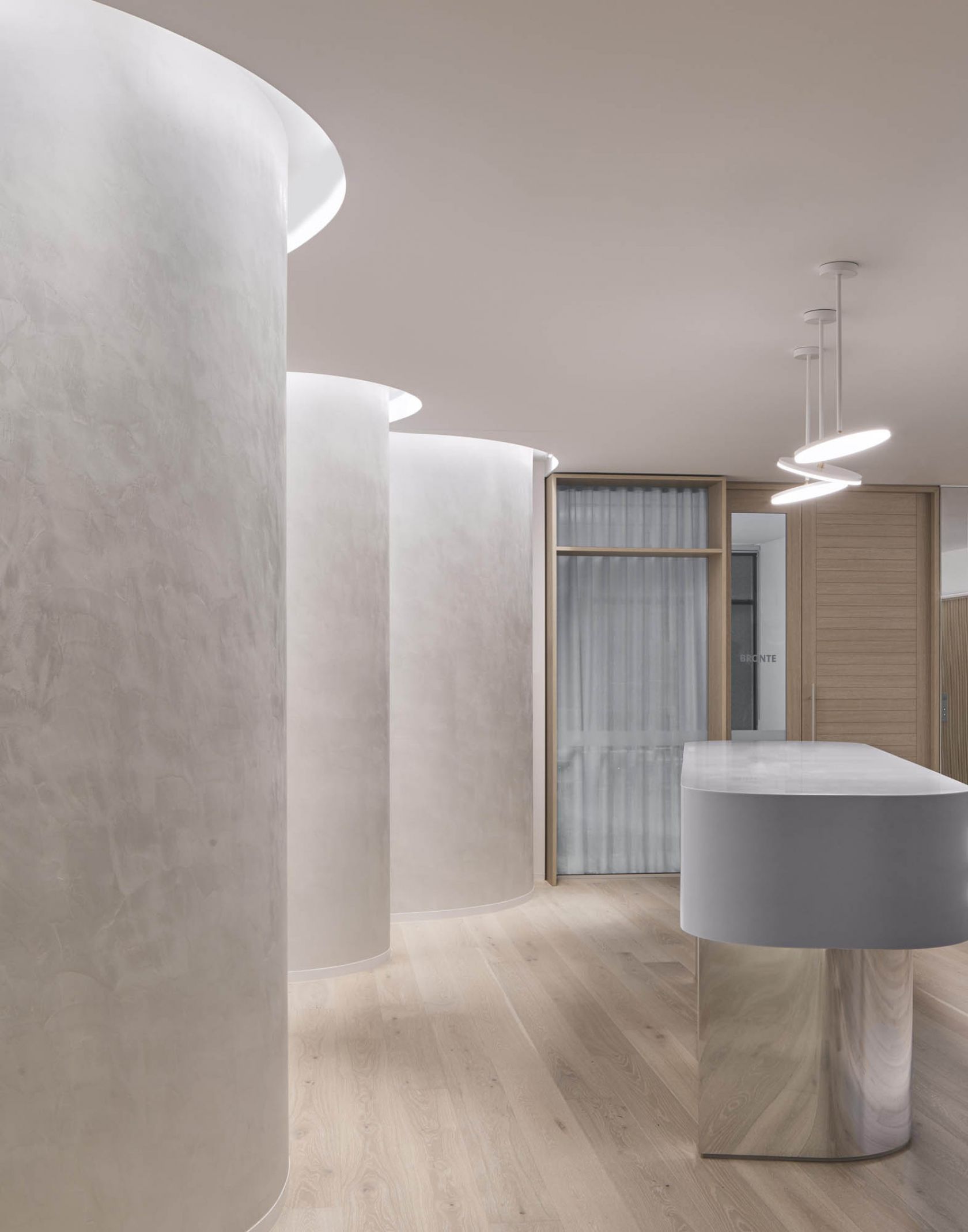
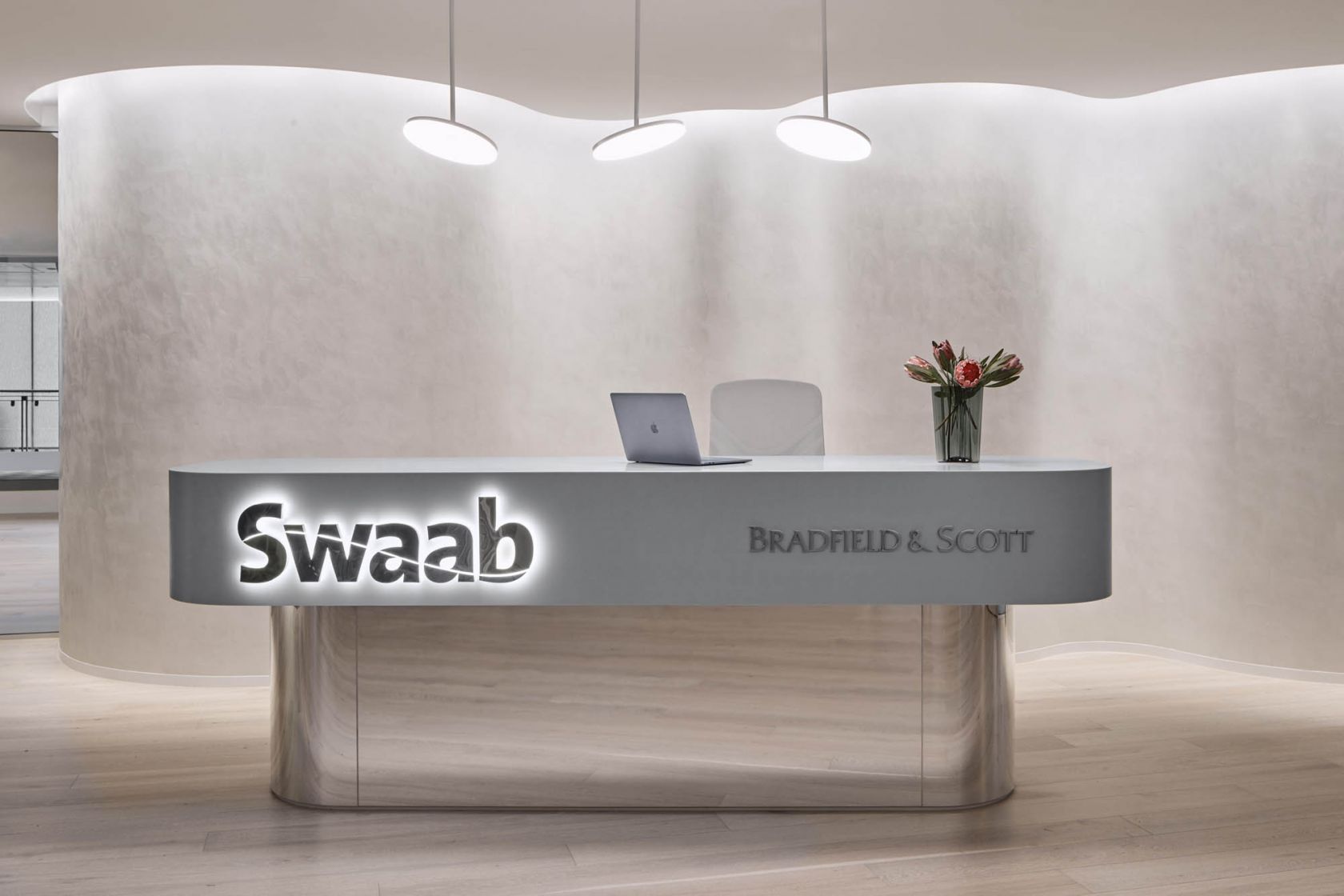
Streamlined delivery
A staged delivery across three floors ensured that Swaab’s team could continue to operate within their existing space throughout the project’s delivery.
It was also of benefit to delivery, with our team being able to carry forward critical construction knowledge and lessons learnt after the completion of each stage. In particular, this allowed for the condensed development and construction of architectural focal points such as joinery and perforated feature ceilings.
As part of our learnings, we could also begin to anticipate potential challenges, while work-shopping solutions without impacting on the programme. This was particularly evident throughout the COVID-19 restrictions - despite a significant reduction in on-site personnel, our lessons learnt helped to keep the project on track.
The result was a streamlined delivery, enabling Swaab to move in to their new floors sooner than expected.
Virtual tour of Swaab's office fitout
Working with a compromised floor
As the old floorboards were carefully lifted, our team found that the slab’s leveling compound beneath had been compromised. Likely due to a poor mixture applied many years prior, large pieces of the compound were dislodging with each board, leaving cracks and undulations of up to 20mm.
To ensure the new boards wouldn’t be impacted, our team sought to further identify weakened areas across the tenancy. This was done by systematically inspecting each square inch and manually tapping the floor with a hammer to hear if the area had been affected.
These sections were then ground back and meticulously re-leveled to ensure the slab was free from undulations, ready for the new boards to be laid.
Schiavello worked assidiously from day one to understand and prioritise our needs. Their experienced and dedicated team moved heaven and earth to deliver our total refurbishment on time and on budget with no interruption to our business, even with the onset of the unprecedented global pandemic. The quality and standard of their work is excellent. Our people and our clients have been full of praise and positive feedback on our fitout and we are delighted with our new workspace.
Mechanical upgrade
Delivering a full upgrade of Swaab’s mechanical system within a live environment was a unique challenge. Akin to swapping out your car’s engine while driving down a freeway, it required a strategic approach.
In close collaboration with Swaab and with strict coordination between trades, we identified specific zones and down times to minimise the impact on staff.
To ensure adequate air supply would be maintained to all areas throughout the process, our team conducted readings of the sensors and air-flow following each install.
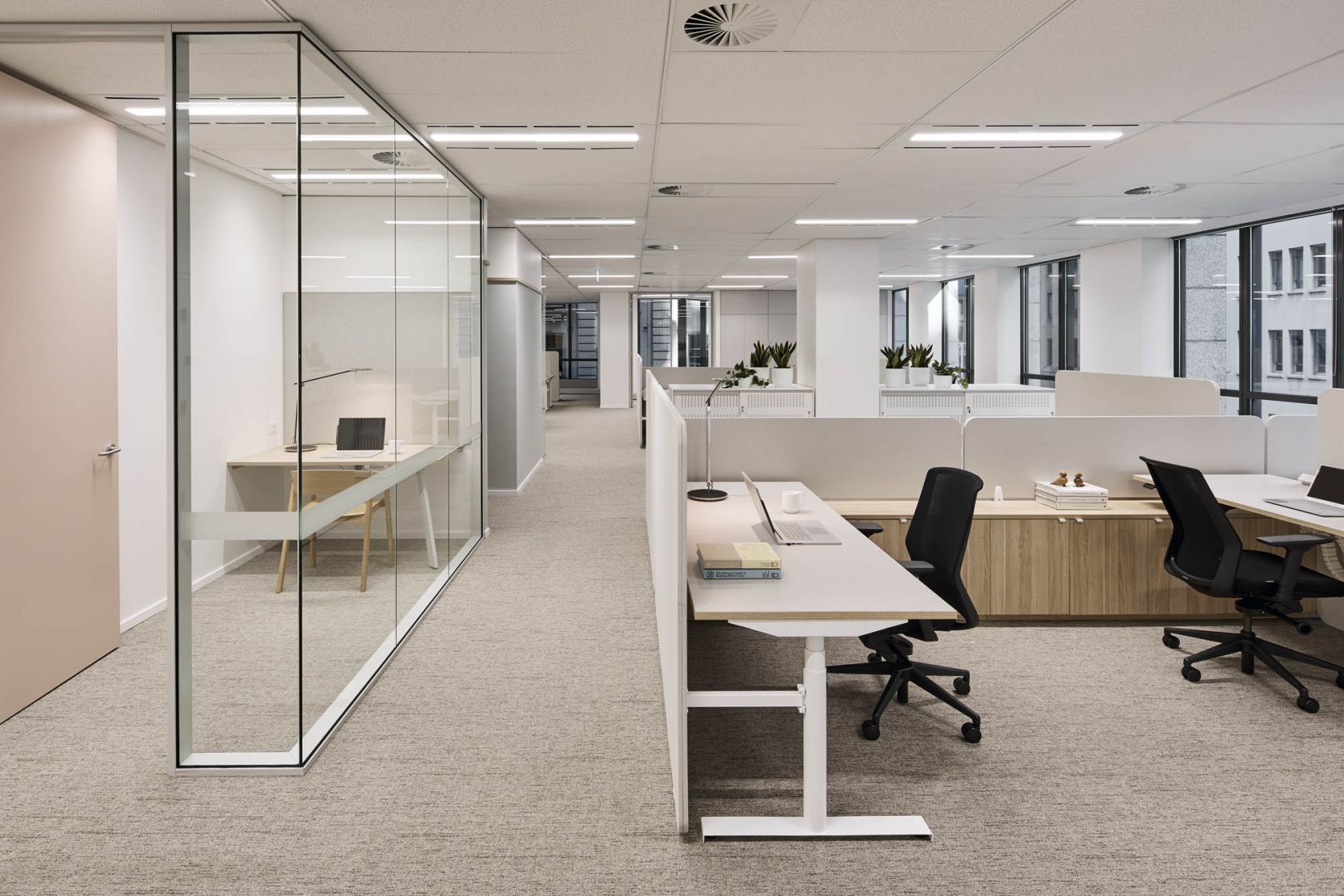
Bringing Bondi into the workplace
Careful choreography of light, form, and materiality throughout the workspace pays homage to founder Fred Swaab's love of Bondi Beach. As Project Manager David Rinaldi explains, these design cues are seen most prominently in the rendered feature wall stretching across the reception.
"The feature wall was designed to mimic a wave, so it was critical to keep the wall looking as natural and organic as possible. We were able to frame out the desired curves on-site using a steel tracking system along the floor and ceiling," says David.
“Framework studs were then installed and tightly positioned to ensure the wall would maintain its form and remain structurally sound once complete. We then wet flexible 6.5mm plasterboard which allowed it to be bent to the desired radius and set in place against the framework,” he adds.
Once primed, our craftspeople applied render to the plasterboard, evoking a sense that the wall has been hewn from a monolithic form rather than assembled from thin surface finishes.
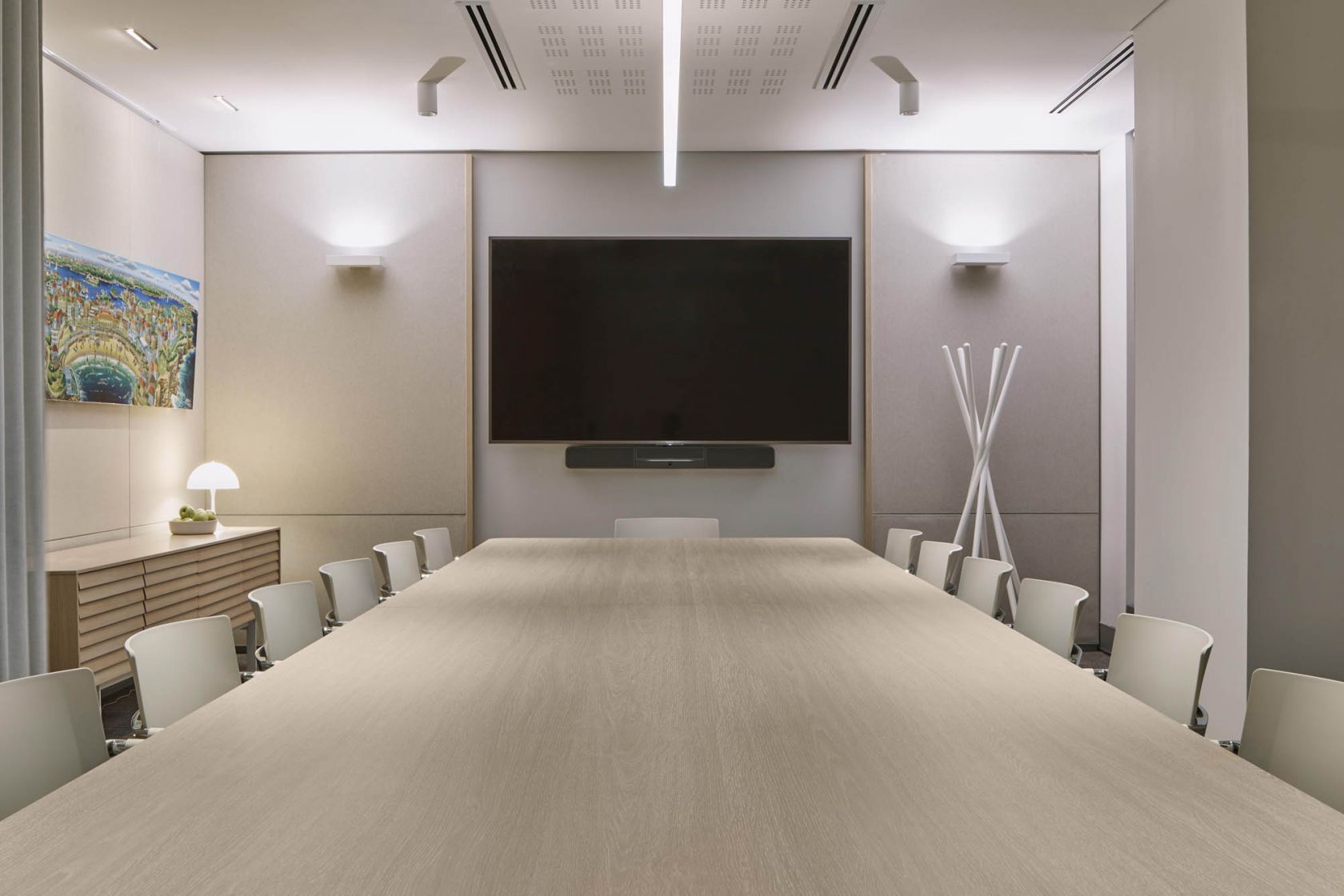
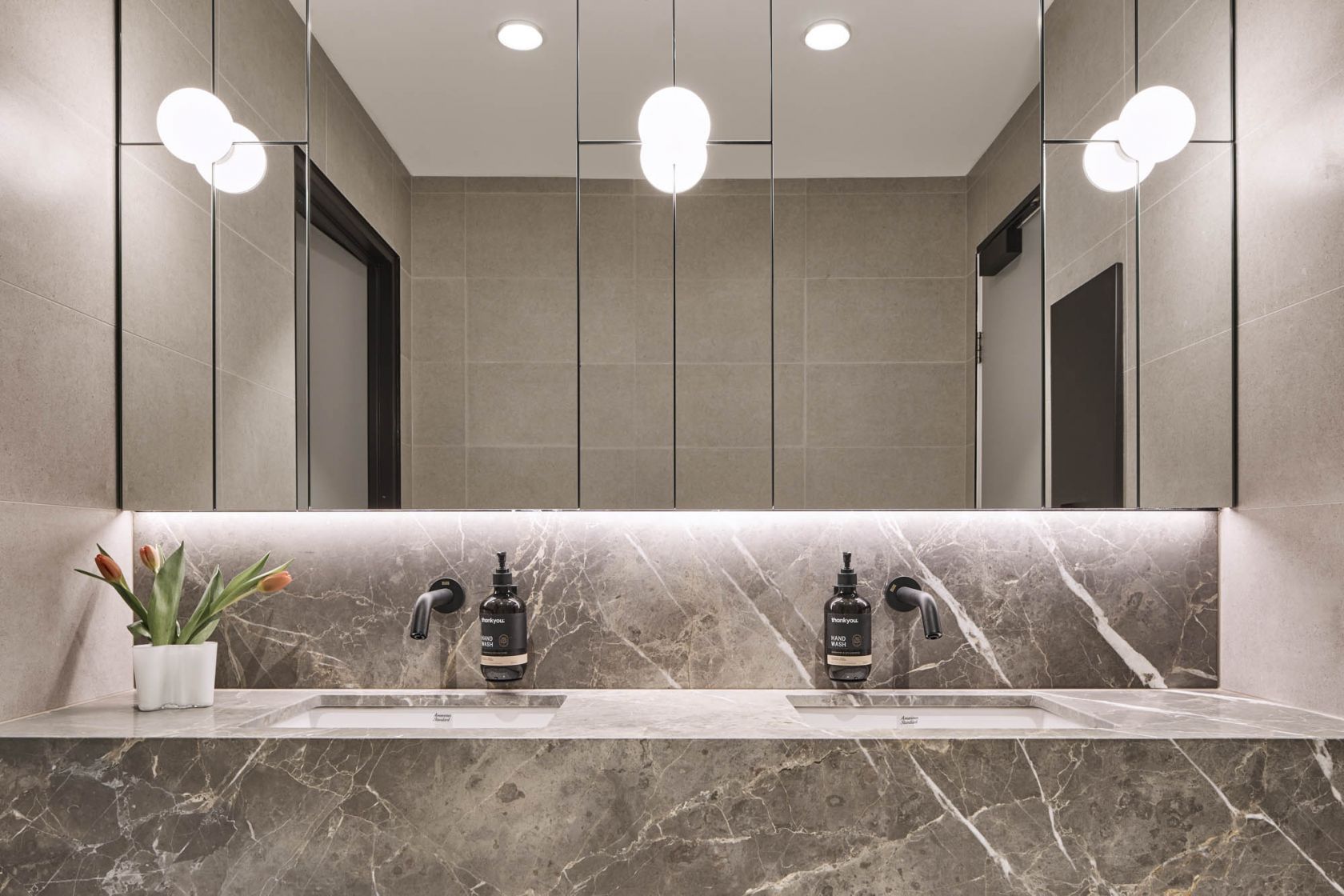
Change champions
As an evolution from traditional to open plan, we worked hand-in-hand with Swaab’s ‘Change Champions’ on-site to encourage staff ‘buy in’ of their new workplace. By involving them in decision-making and providing site tours throughout the build, they were able to share positive feedback with the wider team. We also developed periodic flythrough videos to allow staff to follow the transformation.
Our collaborative approach ensured the journey from the old to the new was seamless for the entire Swaab team; allowing them to embrace their revitalised workplace before even settling in.
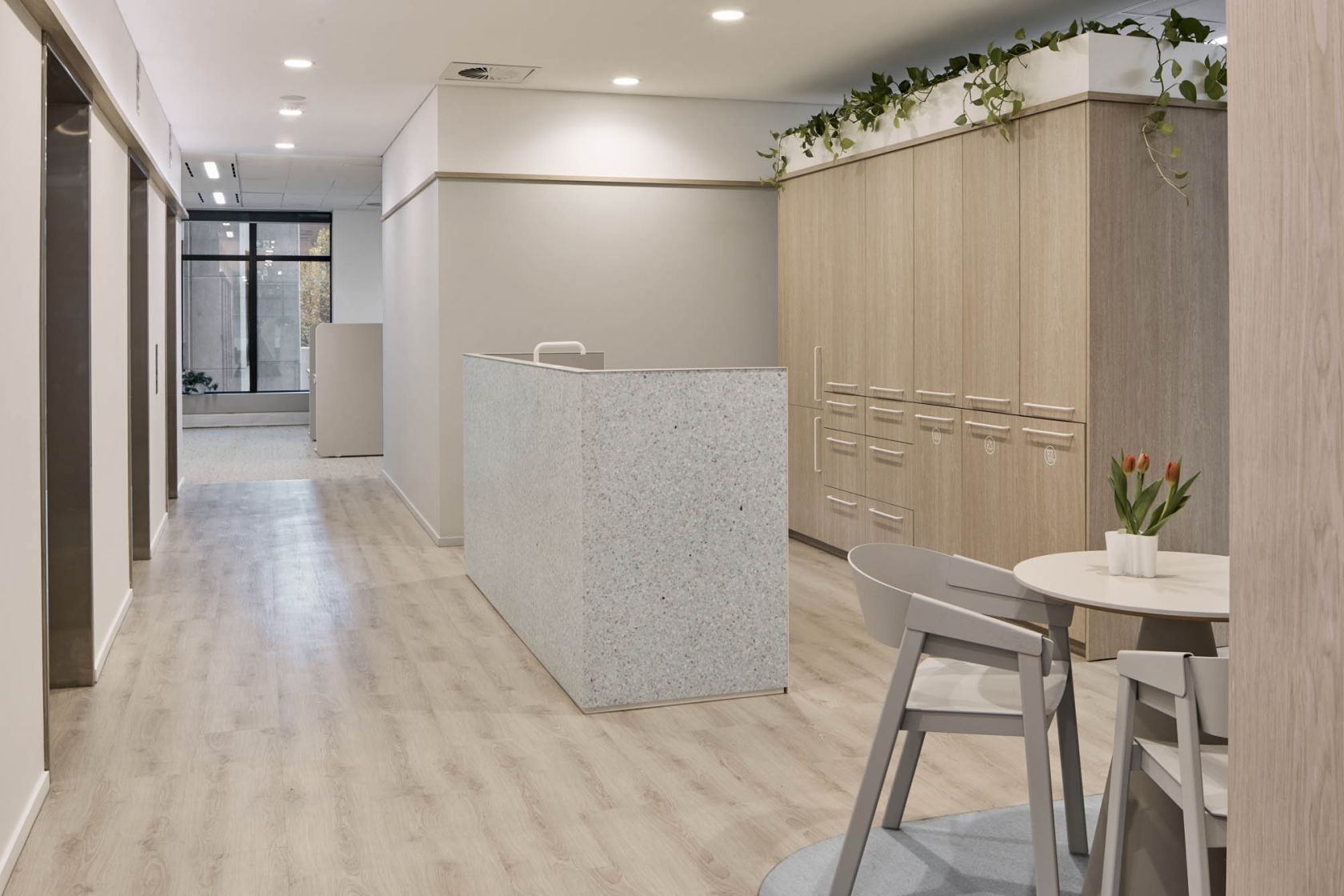